From the forest to the living room
How the world inspires us
Every day at Schattdecor we have one goal in mind: the reproduction of reality. We want to see, feel and experience all elements of nature more intensely. We believe that we achieve the best results when we manage to make nature, through our decors, touch all our senses.
This goal leads us to lie down on the floor of an abandoned building. We close our eyes. We Move very close to 100-year-old elm boards to see whether we can bring out the unique play of colors in the wood.
"It is our employees and their ideas, their understanding of customer needs and their willingness to try new things that enable us to constantly set new impulses globally and to react so agilely to the changing needs of the markets."Christian Zaha | Head of Decormanagement Schattdecor AG, Thansau/Germany
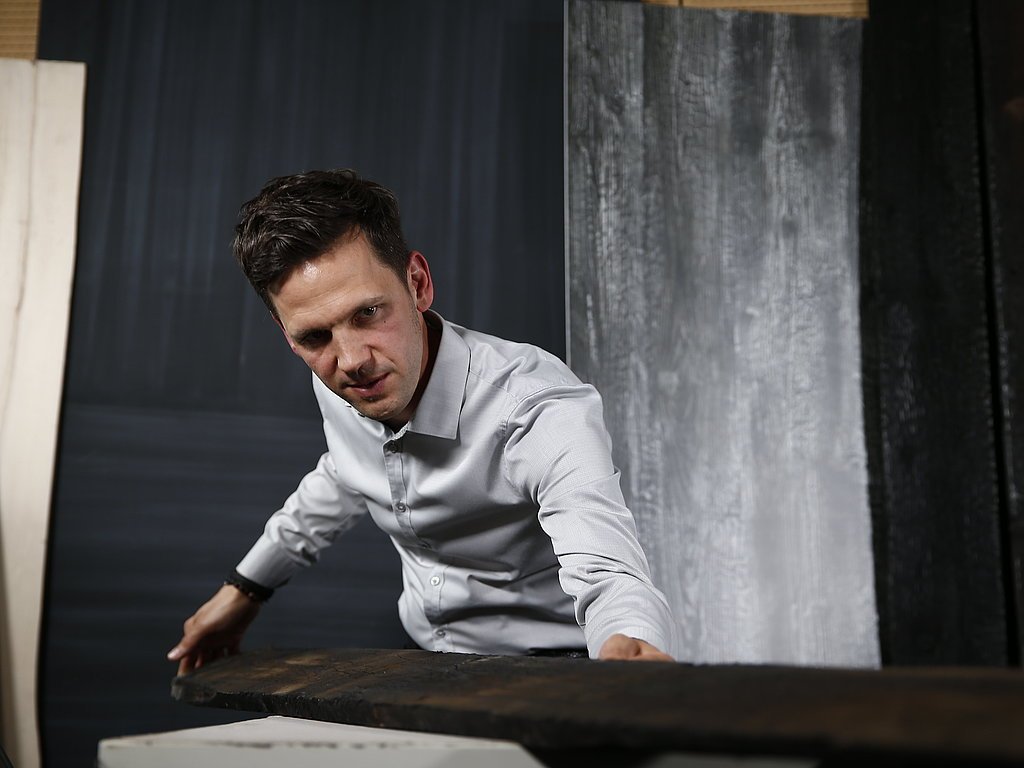
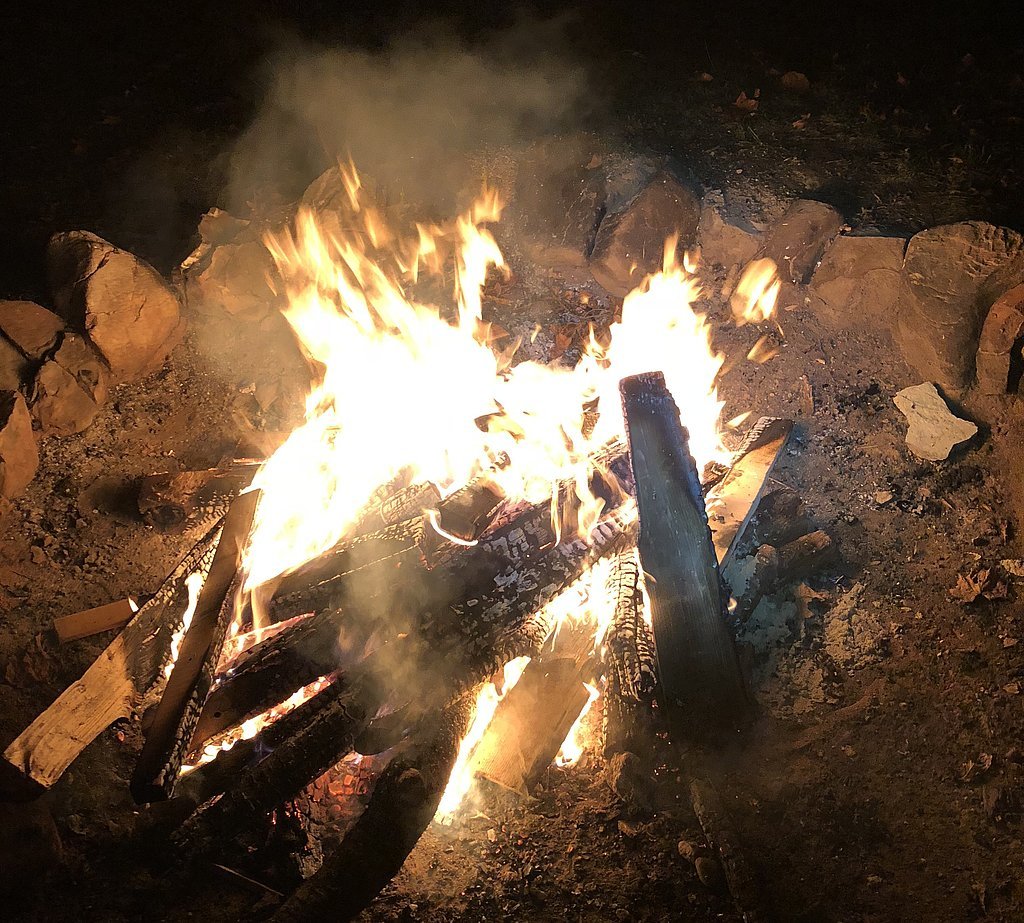
The perfect replica
Our pursuit of naturalness is the reason why we let our palms brush the unique surfaces of our earth every day. That is why nobody at Schattdecor is surprised when a colleague leans over a surface very closely to see more: more of the beauty of nature, more of the perfect reproduction.
But it is also the vision of cool designs and the expertise in surfaces of all kinds that show us the way to hidden treasures. For example, there is a Persian limestone, which now illuminates furniture fronts and countertops as a noble stone decor called “Grey Caspio”. It is the sense for foreign cultures and trends that prompts us to burn wooden planks in our own garden in order to let the “Black Glow” decor rise like a phoenix from the ashes.
Our passion for beautiful things gives us a kind of permanent motivation to step out of our comfort zones and focus our eyes on new, unknown, perhaps still undiscovered things. As if the world were a gigantic work of art. A huge playground for perspectives.
From the forest to the resource bank - and then to reproduction
Many departments work closely together to create a gravure printed decor. The basis for a new decor, which for example shimmers in the play of light and shadow as deep and versatile as the original, lies in the reproduction (repro for short). Here raw materials such as solid wood, veneers or stones are collected and stored in a kind of library.
For example, if a new floor decor is to be developed, a test scan is first carried out on an extremely high-resolution scanner with various lamp settings. "A one-sided exposure, for example, creates a relief-like structure. The position of the original on the scanner and thus the distance between the lamp and the surface make a decisive contribution to the drawing, the 3D effect and the color", says Helmut Demegni.
A matrix is created from the interaction of the lamp configuration with the respective surface treatment. These results are then evaluated and the desired optics are selected.
After the optics have been selected, the so-called stock is selected in the final scan (a selection of the best sections). The same processing steps are then carried out as for the test template with the necessary scanning. A lot of experience is required to implement a decor idea with the prepared material into a coherent layout concept. The composition of the flower and stripe areas, the arrangement of knots and cracks as well as the homogeneous distribution of the different planks over the entire layout are decisive here. To create the layout, the scans are printed out in their original size and reassembled with an optimized aesthetic. This is the so-called hand layout.
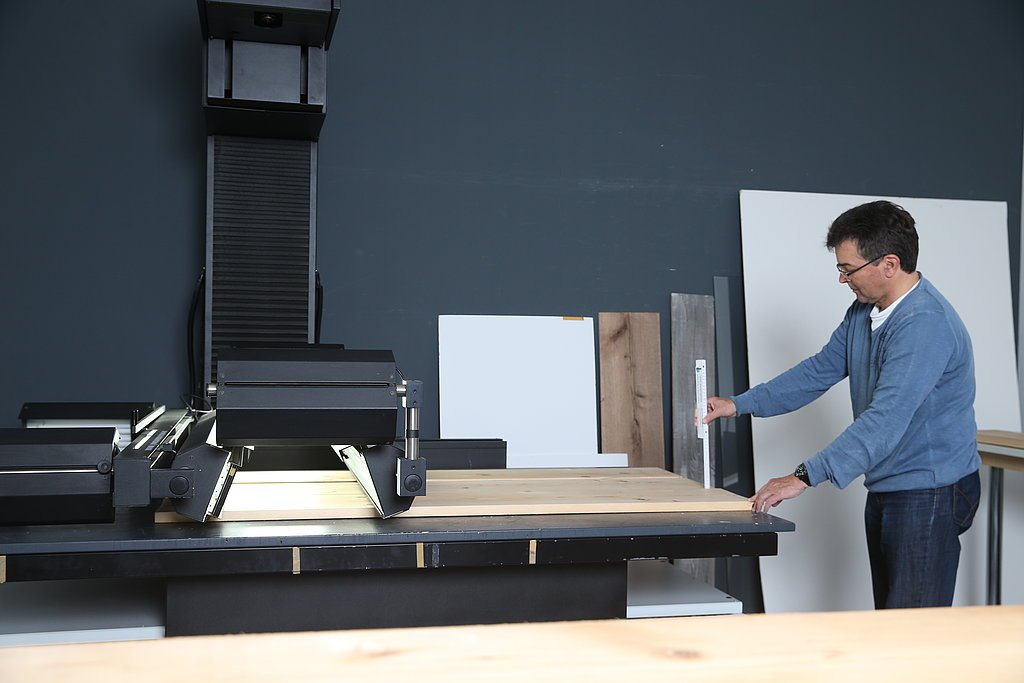
The optimized original thanks to color-true monitors
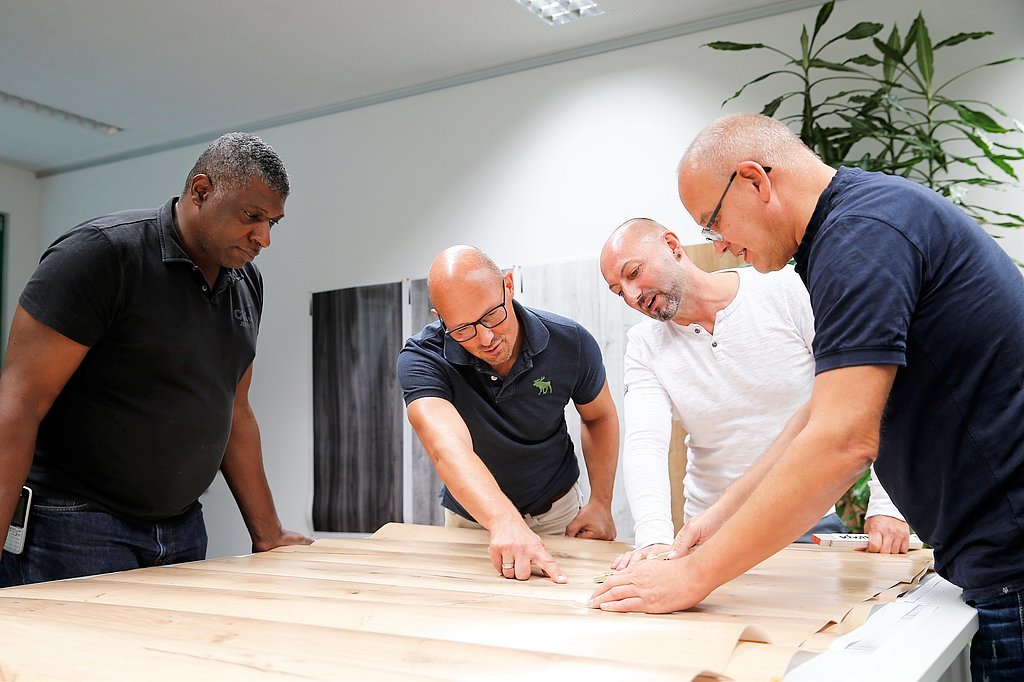
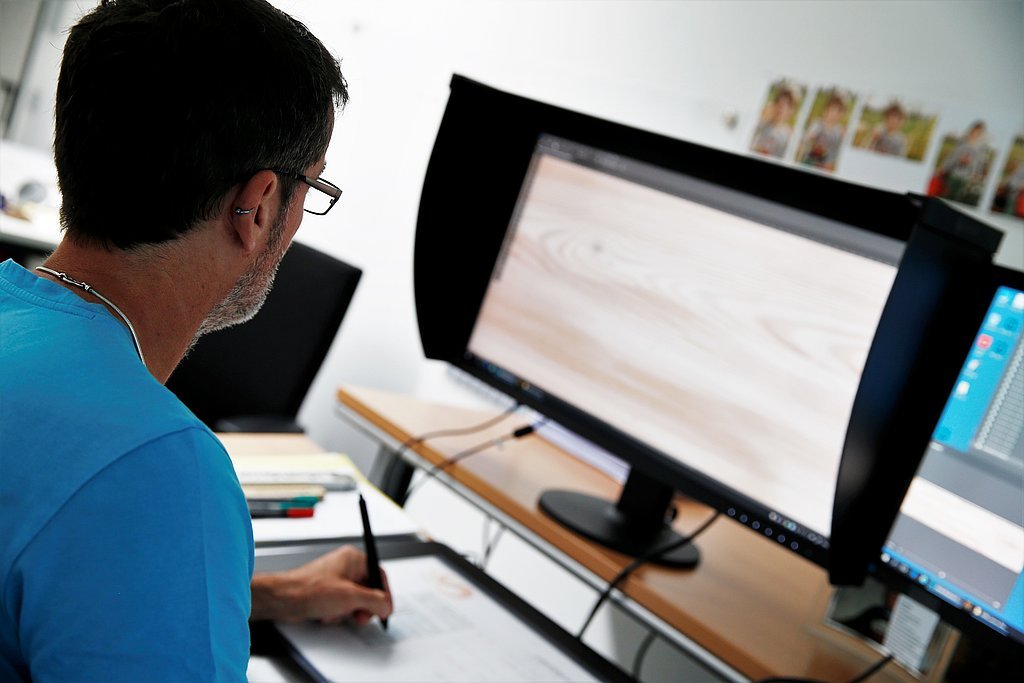
Off to the next department, the so-called "operator". The color-calibrated graphics monitors can definitely do more here. The team works on the layout design at its highly specialized workstations using professional programs in such a way that at the end the exact color information for each of the four gravure cylinders is available as digital information. The process of dividing the scan file into four individual files is called separation. Provided with the appropriate mixed colors, they are superimposed on the color of the original layout. Put extremely simply: The operator team, with their exceptionally good imagination and feeling for colors, ensures that each cylinder of our decor printing machines knows in which order what depth of the wood structure and in what color on the decor paper the design should be printed.
Ready – Set – Print
Now the time has come: The design, decor development and sales departments discuss the finished layout and provide feedback on the wood structure, retouching or coloring. If the approval is given, the machines start up production.